Page 1 of 1
Babbiting
Posted: Thu Apr 11, 2019 8:51 pm
by D.Yoder
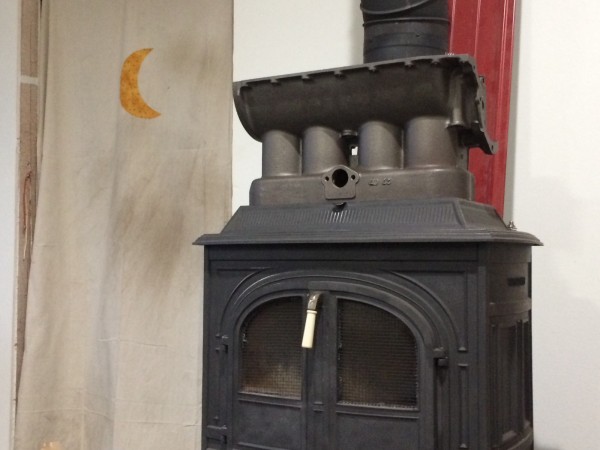
- Preheat
Re: Babbiting
Posted: Thu Apr 11, 2019 9:11 pm
by John E. Guitar
That stove looks tailor-made for the job!
Re: Babbiting
Posted: Thu Apr 11, 2019 11:34 pm
by KeithG
How many T Guys have a wood stove in their house with a T block on top of it?
Don't everybody stand up at once....
Keith
Re: Babbiting
Posted: Fri Apr 12, 2019 12:10 pm
by D.Yoder
Keith, what I want to know is how many T guys have a moon applicayed to there bathroom

door?
Re: Babbiting
Posted: Mon Apr 15, 2019 11:34 pm
by Kohnke Rebabbitting
We don't have a stove either. But when I was a kid, we could have used it in the out house, in the winter. We have been using the No. 35 torch, 45,000 BTU's . Cutting torches, have no place in babbitt bearing work. We Have used that for over 50 years. I thank the one now is the third new one.
http://www.johnsongas.com/industrial/ms-torch.asp
Herm
Re: Babbiting
Posted: Mon Apr 15, 2019 11:46 pm
by John E. Guitar
Herm, thanks for posting these photos of your rod pouring setup. How do you pour in the babbit and what speed does the rod rotate at?
Re: Babbiting
Posted: Tue Apr 16, 2019 1:46 am
by Kohnke Rebabbitting
John E. Guitar wrote: ↑Mon Apr 15, 2019 11:46 pm
Herm, thanks for posting these photos of your rod pouring setup. How do you pour in the babbit and what speed does the rod rotate at?
We pour with a Ladle with a snout, of varying lengths.
It runs at about 1,200 R. P. M's.
Re: Babbiting
Posted: Tue Apr 16, 2019 1:49 am
by Kohnke Rebabbitting
Pictures.
Re: Babbiting
Posted: Tue Apr 16, 2019 3:07 am
by John E. Guitar
Thanks for that Herm.
We sell an aluminium drive spider here that we have to do some machining on to fit a particular application. The supplier is Italian but they shifted production to China a few years back. One of the things that took place in the shift was that they stopped using centrifugal casting. It was surprising to see how much porosity there was in the castings once they made that change. We stopped using those guys not long after.
Re: Babbiting
Posted: Thu Apr 18, 2019 12:53 am
by Kohnke Rebabbitting
Pictures.
This is the heating torch we use to heat Jigs, Blocks, ect.
Herm.
Re: Babbiting
Posted: Thu Apr 18, 2019 6:58 am
by Joe Bell
It looks real interesting but I bet you have to be suited up well from flying Babbitt!
Re: Babbiting
Posted: Thu Apr 18, 2019 12:19 pm
by Mark Gregush
how do you get the babbitt into the bearing when pouring? Horizontal I might understand, but vertical not so much.
Re: Babbiting
Posted: Thu Apr 18, 2019 1:57 pm
by Kohnke Rebabbitting
Mark Gregush wrote: ↑Thu Apr 18, 2019 12:19 pm
how do you get the babbitt into the bearing when pouring? Horizontal I might understand, but vertical not so much.
Most casters are vertical, or you also having to over come gravity. They are also easier to set up, and work on.
For pouring babbitt, we use a Ladle with a 3, or 4 inch spout, to go inside the Die opening.
Herm.
Re: Babbiting
Posted: Thu Apr 18, 2019 6:37 pm
by Kohnke Rebabbitting
Suited up, yes indeed, Welder cap, long sleeve insulated shirt, and Face shield, babbitt is 950.
On the opening side, floors, walls, and ceiling, and me, if I get a little complacent.
With out the spinner, we couldn't pour all the thin wall cam bearings, bronze, and steel out of all the car brands, like Packards, Buicks, electrical bearings, Ect., as we have found that we can't pour cam bearings statically, as when they cool, the out side shell cools first, and then when the babbitt cools, as it shrinks to the inside center, and then breaks the tinning bond from the shells wall. You can even hear it clink, sound.
On Model T cam bearings, we drill 3 lines of 1/8th holes, one line down the center, and the other two lines just under the part lines. Doing this, after being spun, the babbitt is tight, like, or better then peening from centrifugal force, and made the babbitt very tight around all of the bearings edges. The anchor holes, and the original Broached grooves, are not there to hold in the babbitt, they are there to keep the babbitt from spinning, in use. The babbitt in static poured T bearings, are normally loose.
Also, when you take out old cam bearings, ( not Model T 's ) the bearing when new was a larger diameter, for crush. So, when you put a hot shell bearing in a spinner, it is at the diameter it was originally, and when you put in the babbitt, it pushes against the shell, and holds it there, until, it hardens. You don't want loose cam bearings.
OK, I have told you more then I know !
Herm.