Page 1 of 1
Axle Gears
Posted: Sat Jun 04, 2022 11:05 am
by Oldav8tor
A couple of friends are tearing their car's rear ends apart and will be replacing the axles. What kind of rig is required for pressing the existing axle gears off and installing the new ones? Is it something we might put together from reasonably priced components or a job best left to the experts?
Re: Axle Gears
Posted: Sat Jun 04, 2022 11:08 am
by 1923Touring
I used a harbor freight 20 ton press without a problem. I did have one particularly stuck gear that required penetrating oil all night before it pressed off. Hope this helps.
-Joshua
Re: Axle Gears
Posted: Sat Jun 04, 2022 11:14 am
by RajoRacer
First you need to press the gear farther on in order to remove the split locks then press the gear off - they can be a bugger ! I clean & dress off the inside of the gear prior to installing on a new axle - I also utilize a "cage" & a spare hub for pressing the gear back on - same drill - one needs to press the gear on far enough to insert the splits locks then press back down the axle to seat it. I also use anti-seize.
Re: Axle Gears
Posted: Sat Jun 04, 2022 12:02 pm
by Dropacent
All good hints ! I always clamp some angle iron to the shaft, and TRUST BUT VERIFY dimensions of the new parts. Read up on press fit tolerances.
Re: Axle Gears
Posted: Sat Jun 04, 2022 12:14 pm
by henryford2
Good advice Tim. I replaced the rear axles on two cars last year. I found the axles from Snyders (they may be making them for all the vendors at this point in time) where dead on the money. No issues going on.
Re: Axle Gears
Posted: Sat Jun 04, 2022 12:52 pm
by John kuehn
If you have determined that the axles are worn to bad cut them off to around 4-6” and press them off that way. Some presses won’t allow you to be able to put the entire length of the axle to fit in the press.
Good luck installing the new axles and ALWAYS make sure your gears are just a few thousandths larger than your axle.
DONT ASSUME they will easily go together. For an example you can’t press a 1” dia. shaft into a 1”dia hole. IT WILL NOT WORK,
I bought a new axle and learned the hard way by bending the shaft. I didn’t check the gear I D
Before I tried to press on the gear.
REMEMBER there is some variance in the ID of the gears. Ford allowed some on the gears and also the OD on the shafts.
The same goes for new axles also.
Good luck and remember to check the clearances of the shaft and the gears.
Re: Axle Gears
Posted: Sat Jun 04, 2022 1:07 pm
by RajoRacer
Also - if you're installing new axles (I believe Snyder's is the only manufacturer), verify the 1/4" key stock you'll be using - "off the shelf" key stock has been too large for the newly machined keyways !
Re: Axle Gears
Posted: Sat Jun 04, 2022 1:32 pm
by Scott_Conger
Adding to Steve's good advice, I'd say examine and ensure that ALL new axle dimensions related to fitting the gear are Kosher...they aren't always...
if dimensions are over size even a couple tenths, you'll play the devil trying to press the new gear on...
Re: Axle Gears
Posted: Sat Jun 04, 2022 1:54 pm
by speedytinc
To press the gear down, especially the first time, I put the axle nut on backwards all the way to the thread end & put in a thick wall 1" ID pipe/tubing with a 10" square plate welded on the bottom to prevent it from bending. 20 ton press.
Re: Axle Gears
Posted: Sat Jun 04, 2022 1:56 pm
by KBurket
I broke an axle in 2019 and bought two new ones from Chaffins garage. I bought a 20 ton press from HF. I used a 1” tube as a safety brace. One gear was stubborn but both came off with this set up. I used a large socket, augmented with a stack of right sized washers to press the gear on so I could get the lock off. Then a smaller deep socket to press the axle off the gear.
I replaced the ring and pinion gears, axle bearing sleeves, and a few other things while I had the rear ended off of the car.
Re: Axle Gears
Posted: Sat Jun 04, 2022 3:19 pm
by RGould1910
When pressing the axle gear down to expose the split lock rings and when pressing the gear on the new axle, first insert the tapered end of the axle in a rear wheel hub. It will keep the axle from bending. Im surprised this hasn't been mentioned
Re: Axle Gears
Posted: Sat Jun 04, 2022 3:42 pm
by RGould1910
Oops I see Steve mentioned using a spare hub.
Re: Axle Gears
Posted: Sat Jun 04, 2022 6:15 pm
by Speedsterguy2
I generally agree with the process that most all postings give. I did do a couple of things differently. I have a 12 ton Harbor Freight press, which I modified with spacers to tighten against, around the bolts in the top and bottom of the frame, and brazed in shims in the cross slide to get a tighter fit and maintain squareness (see photo below). I also used a toaster oven to get the gears warmed up before pressing gears onto new axles. Oven setting tops at "400-500 F". After 2 hours, a digital laser thermometer said 375 degrees, which was close enough (not hot enough to affect the temper of the steel). Gears all went on fine, and the new axles (from Langs) are finished to a great quality. It is important to get the ram on the press centered on the gear, get the axle vertical and centered, and watch what you are doing so as to not get something cocked or bound up.
I disassembled 7 rear ends in my quest to build 2 good Ruckstells. The axle gears were in fairly bad shape on many of them. Many were severely scored on the thrust surface, and many had significant wear on the outside diameter of the shoulder. Specifications say the axle gear holes are supposed to be 1.812", and the axle gear shoulder is to be 1.806-1.807", giving a clearance of 0.005-0.006". I found gears worn as small as 1.803", but also some as large as 1.810", larger than they are supposed to be. Yes, my tool is a vernier caliper, but I am measuring the hole I.D. and the gear shoulder O.D. with the same tool, so the clearance readings should be correct.
I did find the axle gear internal to be scored on many gears also. Several hours with 220 grit carborundum paper, followed by 600 grit paper on the tips of my now worn fingers smoothed out my 4 chosen gears to prepare them to install. I also used the same sanding paper on the thrust face of a couple of the gears. Yes, it takes quite a while. The other thing I found was some gears stamped with "-1, -2, -3" along with the Ford logo (see photos). I have never heard discussion of these numbers on axle gears. It would seem logical that Ford had recognized that some axles were fat, and some gears were tight, so perhaps had a system to allow assembly workers to match up axles and gears with the least amount of trouble. I did measure gear I.D's and axle O.D.'s and matched up pairs to fit best as I could. Though, the numbers could relate to gear shoulder O.D. instead of hole I.D.....
In the end, all went together well, without needing excessive force, and the 12 ton press did fine. I think heating in the toaster oven helped things to go smoothly too.
Re: Axle Gears
Posted: Sat Jun 04, 2022 8:17 pm
by Oldav8tor
Hmmm.... I don't think I have it quite straight in my mind.... I see the advantages of setting the end in a wheel hub (I have a couple) and running it through a pipe for support, but I haven't quite figured out the actual pressing "on" and "off". If you're pushing down on the gear with a socket or pipe or whatever, how do you get to the lock rings to remove them (or install them)? To press the gear off - do you just rest the bottom of the gear against the frame and push the axle itself down once the lock rings are removed? Some close-up pix would be helpful if you have them.
This would be a great subject for a "how to" video.
Re: Axle Gears
Posted: Sat Jun 04, 2022 9:08 pm
by RGould1910
1. Set the axle in a hub and set it in the press with the gear on top
2. Get a piece of short pipe the diameter which fits inside the recessed area inside the axle gear teeth.
3. Place the pipe inside the recess and press on the pipe so the axle gear travels down the axle to clear the locking rings
4. Remove the two locking rings now exposed.
5. Place support under the shoulder of the axle gear allowing room for the axle shaft to clear. I use two metal blocks
6. With the locking rings removed press the axle down thru the gear and out the other end.
To install
1. Place the new axle in the hub as before
2. Press on the axle gear after installing the key being careful to align the key with the groove in the gear. Use the pipe described above.
3. Press the gear down on the axle far enough to install the locking rings in the axle
3. Install the rings
4. Place support under the gear sleeve and press the axle stub pertruding above gear down against the locking rings
Tell me is I've missed something
Btw, you dont need a pipe to protect the axle from bending if you use a hub. Using antiseize inside the hubs helps in removal.
Re: Axle Gears
Posted: Sun Jun 05, 2022 4:09 am
by Allan
You may need a pipe to stop the axle bowing when pressing the gear further onto the shaft to remove the keepers. The hub on the end protects the thread and the taper on the axle, but sometimes the load on the gear will bow the axle before the gear will move. Ask me how I know this.
Allan from down under.
Re: Axle Gears
Posted: Sun Jun 05, 2022 8:51 am
by John kuehn
This is an interesting subject and to me it always goes back to how Ford did it. It’s come up before and one post had a good answer or something similar a few years ago.
Since Ford was in production mode there probably was a stack of axles and boxes of axle gears to pick from and assemble each axle.
Did the factory have any issues in keeping the tolerances pretty close?
I have a feeling there was a few bent axles or some gears were discarded because of picking axles that happened to be on the high end of the tolerance scale and a gear that was on the low end. And if that happened in a high production mode something had to give and I’ll bet it was the axle.
And of course quality control was considered but the assembly lines had to keep moving.
Re: Axle Gears
Posted: Sun Jun 05, 2022 10:22 am
by Mark Nunn
I reinforced my axles before pressing gears with 2 pieces of angle iron, about 24" long. I put them around the axle and used radiator clamps to hold them in place.
Re: Axle Gears
Posted: Sun Jun 05, 2022 6:47 pm
by Oldav8tor
I must really be dense. When you describe getting a "a piece of short pipe the diameter which fits inside the recessed area inside the axle gear teeth" wouldn't the pipe block access to the clips that need to be removed?
Or is it that once you've pushed the gear down to clear the clips, the gear stays down after you remove the pressure so you can lift the pipe and remove the clips?
Re: Axle Gears
Posted: Sun Jun 05, 2022 7:33 pm
by Jerry VanOoteghem
Oldav8tor wrote: ↑Sun Jun 05, 2022 6:47 pm
Or is it that once you've pushed the gear down to clear the clips, the gear
stays down after you remove the pressure so you can lift the pipe and remove the clips?
Yup, that's it exactly Tim!
Re: Axle Gears
Posted: Mon Jun 06, 2022 3:19 pm
by Oldav8tor
A picture is worth a thousand words....
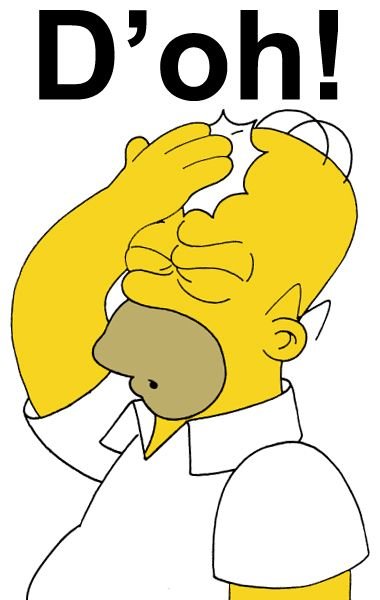
- doh.jpg (32.35 KiB) Viewed 4198 times
Re: Axle Gears
Posted: Mon Jun 06, 2022 3:44 pm
by DHort
I had abou a dozen gears removed from bad axles and put them in a box. If you need any let me know and i will look for that box.
Re: Axle Gears
Posted: Tue Jun 07, 2022 11:07 am
by Oldav8tor
Thanks Dave - hopefully we won't mess these gears up.
Question: One of our club members has a 12 ton press that he's willing to set up to do such jobs. Most of the posts mention a 20 ton. Is a 12 ton hefty enough to do the job?
Re: Axle Gears
Posted: Tue Jun 07, 2022 11:15 am
by speedytinc
Oldav8tor wrote: ↑Tue Jun 07, 2022 11:07 am
Thanks Dave - hopefully we won't mess these gears up.
Question: One of our club members has a 12 ton press that he's willing to set up to do such jobs. Most of the posts mention a 20 ton. Is a 12 ton hefty enough to do the job?
I have had a few that took all 20 with a BANG. You might have a few that wont relent @ 12 tons the majority will. The press frame has to be real stiff. lighter framed presses want to flex & parallelogram.
Re: Axle Gears
Posted: Tue Jun 07, 2022 11:32 am
by speedytinc
My observations regarding all this talk about axle/gear clearance & varying fits. I have worked a lot of these axles/gears. Parting out rear ends & salvaging unloved iron one step away from scrap. I only save the good parts. Must have 40 excellent gears taken from bad axles & 20 excellent axles removed from bad gears. In working with original Ford parts, I find the fit & clearance is the same. A few galled axle/gear meshes take more press pressure to separate, but normally very consistent. That shows me Ford tolerances were very consistent. Switching gears to other axles still press back tight. Of the axles where the gears came off real easy. The axles were unscripted period replacements.
When dealing with new replacement axles, you cant count on the proper fit.