Page 1 of 1
Hyatt Bearings (almost)
Posted: Sun Feb 11, 2024 10:49 pm
by jab35
Those familiar with Hyatt bearings may already know about these modern spiral or helical roller bearings that are currently used in high temperature applications like rolling mills for continuous casting of steel. They resemble the original model T axle and driveshaft spool bearings but are much larger. I do wonder if smaller versions of the rollers might be available. If anyone knows more about these please share. Sincerely, jb
https://www.pun-waelzlagertechnik.de/en ... 1513_2.jpg
Re: Hyatt Bearings (almost)
Posted: Mon Feb 12, 2024 6:08 am
by Jerry VanOoteghem
Interesting! The bearings are larger, but the rolloers appear to be at least near the same.
Re: Hyatt Bearings (almost)
Posted: Mon Feb 12, 2024 6:50 am
by Dan Hatch
USA office is in Covington GA.
Re: Hyatt Bearings (almost)
Posted: Mon Feb 12, 2024 9:12 am
by Art M
I am familiar with the Hyatt wound roller bearings. Hyatt Roller Bearings was a division of General Motors and New Departure Ball Bearings was also a division of GM. The two divisions merged as New Departure Hyatt Bearing Division of GM on March 1, 1965. Sandusky became the headquarters for the Division.
In 1962 I was hired by New Departure as an engineering cooperative student. This allowed me to work in every department in the Division. In 1966 I became an application engineer in the Product Engineering Department.
I must leave this writing at the moment to attend a close friend's funeral. But will continue later.
Art Mirtes
Re: Hyatt Bearings (almost)
Posted: Mon Feb 12, 2024 10:19 am
by jab35
Thanks for your replies. Art, sorry for your loss.
What do you think the demand might be for new, made to Ford spec 'Hyatt' rear axle bearings? Appreciate your feedback. jb
Re: Hyatt Bearings (almost)
Posted: Mon Feb 12, 2024 2:52 pm
by Mark Gregush
It might be good depending on how much people want to spend. Not everyone is going to drive enough to warrant high cost on a car driven a few times a year. I know people come on all the time talking about how easy it is to find good originals because they have a huge stash two pull from, but my findings have been something like, I am lucky to find one or two usable bearings in 10+ that I check and some of those "good" ones might be just under the usable size.
Re: Hyatt Bearings (almost)
Posted: Mon Feb 12, 2024 3:08 pm
by Dan Hatch
The demand will depend on the price.
Everybody wants a rebuilt front axle till I tell them the cost. Then they say they will just go find a good one for $10.
Re: Hyatt Bearings (almost)
Posted: Mon Feb 12, 2024 11:32 pm
by Ken Buhler
You are right Dan, but most of the time " a good one" is determined by appearance and not by using gages to support their choice. I straighten and rebuild front and rear axles and I have found most are bent.
Regarding bearings, years ago, Les Schubert suggested having axles made a few thousandths larger. That would allow the use of spiral bearings that are .005 or more worn. I have about 100 bearings cleaned, measured, and categorized for future use and several of those could serve well with larger axles.
Re: Hyatt Bearings (almost)
Posted: Tue Feb 13, 2024 9:50 am
by Art M
The fixed costs to tool the manufacturing of spiral wound bearings would be simply too high. At Hyatt, square wire was wound on a mandrell to rolled lenghts of 20 feet. These lengths were thru-feed centerless ground, cut to finished roller lengths, carbonized, hardened, then finish ground. The cage manufacturing involved stamping presses, machining the cross bars, etc.
All of these processes are very expensive to tool
These bearings were invented by John Hyatt in about 1895 for the sugar beat industry. Eventually these bearings were used in automotive rear axle bearings.
The advantages of wound roller bearings are the ability to absorb shock, to accommodate some misalignment, and to tolerate a fair amount of contamination (dirt). The downside is they have lower dynamic capacity than a similar size conventional cylindrical roller bearing. I want to calculate the capacity and expected life of these bearings in the outer axle bearing position. The analysis of the inner bearing position is much more involved because of gear loading.
My thought on the replacement of these rear axle bearings is to figure out what it takes to use a solid roller bearing. With some application development, I think that these will last for an acceptable time, but probably not as long as a wound roller type.
The subject of mounted clearances need to be addressed. I will disclose my thoughts, but I predict a fight will develop just like my fight several years ago with setting coils.
This topic needs its own thread.
Art Mirtes
Re: Hyatt Bearings (almost)
Posted: Tue Feb 13, 2024 10:06 am
by Dan Hatch
Art I was hoping someone would jump in and make them for $150 each so my 5 gal bucket full of used ones would double in price from $5.00 each to $10.00 each.

Re: Hyatt Bearings (almost)
Posted: Tue Feb 13, 2024 10:23 am
by John kuehn
One of the major suppliers told me that a T owner was dissatisfied because the solid roller style T axle bearings wouldn’t last because you had to grease them fairly often. As mentioned most T’s dont get driven enough to pay big bucks for nice reproduction Hyatt style bearings. So if the solid roller style are avaliable that’s a choice for the weekend T driver.
So for the average T driver it’s either the replacement style solid roller bearings or keep using good original Hyatts.
When going through old T rear axles the inner bearings are overall better than the outer bearings by the way.
Re: Hyatt Bearings (almost)
Posted: Tue Feb 13, 2024 11:42 am
by Art M
I reiterate, solid rollers will go 10,000 miles or more if properly designed and installed. These outers are fairly easy to change.
It looks like there is no need to do any development at this point because there enough old ones to fill the needs. The wound roller bearings will last longer if they are given at least .005 inch clearance maybe 010 might even be better.
Several years ago, i calculated the brg misalignment due to axle shaft bending. I can't remember but it is at least .004 radians.
Art Mirtes
Re: Hyatt Bearings (almost)
Posted: Tue Feb 13, 2024 12:50 pm
by DanTreace
Art M wrote: ↑Tue Feb 13, 2024 11:42 am
I reiterate, solid rollers will go 10,000 miles or more if properly designed and installed.
Every one of those solid Rollers that I have removed, IMO, show distinct wear out of the pinion ends of the solid roller. Some solid mfg. have 6 and some have more of those tiny pinion ends that are extra axles that turn in the cage, and wear out the cage holes.
The Hyatt Ribbon Roller bearing doesn't use a pinion axle in the cage, the Ribbon Roller can float a tad and that prevents abnormal wear. Of course the cage end rivets can become loose, and that renders a Hyatt bearing useless.
But that solid Roller design can escape the cage holes and bind. Known happening with the large dia. solid Roller driveshaft bearing.
Re: Hyatt Bearings (almost)
Posted: Tue Feb 13, 2024 12:59 pm
by TRDxB2
Art M wrote: ↑Tue Feb 13, 2024 11:42 am
I reiterate, solid rollers will go 10,000 miles or more if properly designed and installed. These outers are fairly easy to change.
It looks like there is no need to do any development at this point because there enough old ones to fill the needs. The wound roller bearings will last longer if they are given at least .005 inch clearance maybe 010 might even be better.
Several years ago, i calculated the brg misalignment due to axle shaft bending. I can't remember but it is at least .004 radians.
Art Mirtes
What's the proper way to tighten loose cages ? Also how to determine if axle sleeves are still good.
Re: Hyatt Bearings (almost)
Posted: Tue Feb 13, 2024 5:23 pm
by bmklawt
I read somewhere on the forums that you could get a copy of the mechanical drawings and specs for the Hyatt roller bearings from the Henry Ford Museum, anyone have that and care to share or know what the drawing numbers are.
The Hyatt roller bearing were the hardest part for me to find when I rebuilt my 1927 Touring, I bought at least 30 bearings before Glen Chaffin graciously sold me 4 good bearing on the cheap.
Besides the wheels and tires on the Quadricycle, I did get to see an original Quadricycle tire once, the Hyatt Roller bearings is the only other part I'd like to see the drawings on, Just for fun.
Re: Hyatt Bearings (almost)
Posted: Tue Feb 13, 2024 5:36 pm
by Flivver
Super interesting.
Re: Hyatt Bearings (almost)
Posted: Tue Feb 13, 2024 5:55 pm
by Art M
The original drawings were drawn with ink on linen clothe. I worked on these in the 60's. They are difficult to make changes and don't reproduce very clearly.
In response to the roller axles (called trunions) wearing on the cage: this is where development comes into play.
I think I have seen solid roller axle bearings without trunions. The cage controlled the rollers
Art Mirtes
Re: Hyatt Bearings (almost)
Posted: Tue Feb 13, 2024 8:25 pm
by DanTreace
I read somewhere on the forums that you could get a copy of the mechanical drawings and specs for the Hyatt roller bearings from the Henry Ford Museum, anyone have that and care to share or know what the drawing numbers are.
To order prints from Benson Ford Research Center, you must use the FACTORY NUMBER.
Here is page with Info on ordering prints: https://askus.thehenryford.org/faq/380538. $30 fee per part.
Ford Price List of Parts has two Factory Numbers for the Hyatt rear axle roller bearings.
p/n 2508 Axle Shaft Roller Bearing, Factory No. T-97. Part listed in Bruce's CD as Type 'D 'chrome vanadium steel, Mar. 1920 price was $1.00/ea.
p/n 2508 Axle Shaft Roller Bearing, Factory No.T-253. Dec. 1926 price was $0.55
Not sure of any difference in Factory No. T-97 and Factory No. T-253. But guess would be the Hyatt brand was used in early years, and later Ford got license from Hyatt to make the "Ford" style Hyatt, as you see lots of Ford branded Hyatts.
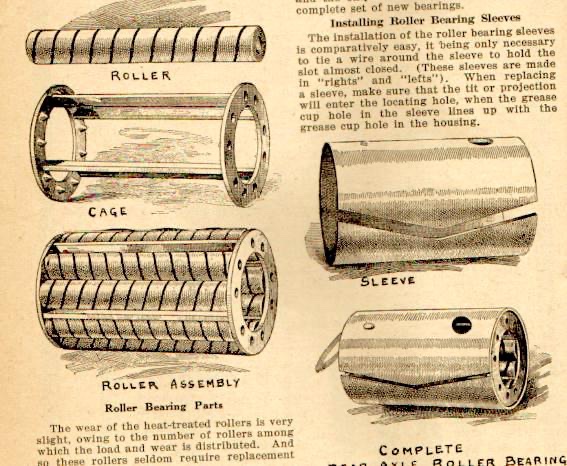
- Hyatt bearing assembly.jpg (128.37 KiB) Viewed 7347 times
Re: Hyatt Bearings (almost)
Posted: Wed Feb 14, 2024 11:19 am
by Susanne
Art M wrote: ↑Tue Feb 13, 2024 9:50 am
The fixed costs to tool the manufacturing of spiral wound bearings would be simply too high. At Hyatt, square wire was wound on a mandrell to rolled lenghts of 20 feet. These lengths were thru-feed centerless ground, cut to finished roller lengths, carbonized, hardened, then finish ground. The cage manufacturing involved stamping presses, machining the cross bars, etc.
All of these processes are very expensive to tool.
Art,
This was the exact problem I discovered. I had (mistakenly) thought they wouldn't be that difficult to produce, and boy, was I wrong! A LOT of specialized processes went into making them, and while form the outside it seems simple, it would be anything but... Add to that the cost of tooling to build them... Yikes!
I even went so far as to talk to one of the production guys at the local metalworking plant, and he started doing some bootstrap figuring on materials, tooling, set up, ordering stock, hardening and machining, and when it was in the low to mid 6 figures (and he wasn't done yet) I told him never mind. trying to do something like that on a piecework basis in my home shop? To the degree of precision which I didn't realize these have??
I must have been mad!

Re: Hyatt Bearings (almost)
Posted: Wed Feb 14, 2024 12:44 pm
by fbergski
What grease is best for Hyatt bearings? I've been using automotive wheel bearing grease in mine, will this suffice?
Re: Hyatt Bearings (almost)
Posted: Wed Feb 14, 2024 2:27 pm
by TRDxB2
fbergski wrote: ↑Wed Feb 14, 2024 12:44 pm
What grease is best for Hyatt bearings? I've been using automotive wheel bearing grease in mine, will this suffice?
Re: Hyatt Bearings (almost)
Posted: Wed Feb 14, 2024 2:40 pm
by DanTreace
Those inner Hyatt's get lubed from the rear axle lubrication, usually 6000W.
The outer Hyatts get lube from filling and turning the grease cups, a good wheel bearing grease, like Valvoline universal red type is just fine.
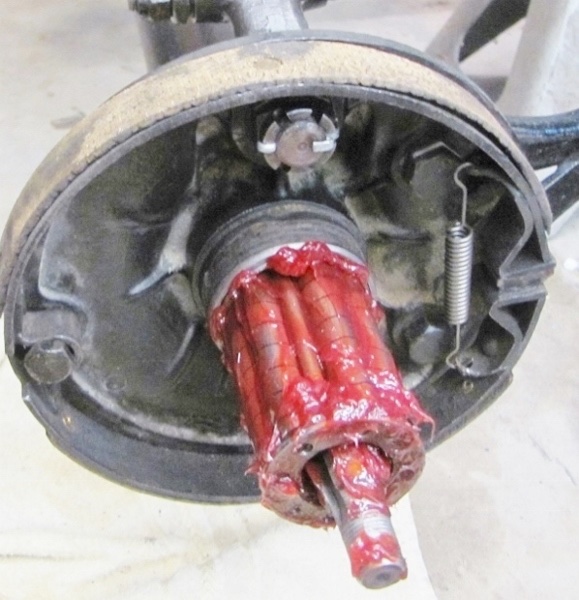
- IMG_2157 (617x639) (603x625) (598x620) (579x600).jpg (143.84 KiB) Viewed 7174 times
Re: Hyatt Bearings (almost)
Posted: Wed Feb 14, 2024 9:55 pm
by Art M
Susanne,
The cost that was presented to you included only the tooling cost. The remaining costs to manufacture include machine capital depreciation and factory burden. And then there is the sales costs.
Art Mirtes
Re: Hyatt Bearings (almost)
Posted: Thu Feb 15, 2024 12:29 am
by Susanne
Don't forget skilled labor and, of course, the government's cut and fuel use/surcharge, warehousing of materials until used, of course the factory owner's profit (they always gotta make something), the list kept growing.
It was not a pretty sight...
Re: Hyatt Bearings (almost)
Posted: Thu Feb 15, 2024 12:37 am
by TRDxB2
Susanne wrote: ↑Thu Feb 15, 2024 12:29 am
Don't forget skilled labor and, of course, the government's cut and fuel use/surcharge, warehousing of materials until used, of course the factory owner's profit (they always gotta make something), the list kept growing.
It was not a pretty sight...
Skilled labor? Whats that?
Re: Hyatt Bearings (almost)
Posted: Thu Feb 15, 2024 10:00 am
by jab35
Thanks for all the thoughtful discussion, I learned a lot of technical information from this thread. Going forward, it seems investing in Bitcoin will likely be more profitable than launching a bearing manufactory. Sincerely, jb
Re: Hyatt Bearings (almost)
Posted: Thu Feb 15, 2024 10:42 am
by TWrenn
jab35 wrote: ↑Thu Feb 15, 2024 10:00 am
Thanks for all the thoughtful discussion, I learned a lot of technical information from this thread. Going forward, it seems investing in Bitcoin will likely be more profitable than launching a bearing manufactory. Sincerely, jb
Ha ha, yep especially since right now Bitcoin is selling at over $52,000! Rumor has it that this is the year it may hit $100K! Hmmmm.
Re: Hyatt Bearings (almost)
Posted: Thu Feb 15, 2024 11:06 am
by Mark Nunn
Making bearing sleeves a smidge thicker would help us use worn bearings.
Re: Hyatt Bearings (almost)
Posted: Thu Feb 15, 2024 11:43 am
by Jerry VanOoteghem
A Hyatt bearing with rollers undersize is not sooo bad. What is bad, is using Hyatts when the rollers are tapered, which is all too common. Tapered rollers will cause the bearing cages to skew/twist, which is what loosens the cages. Tapered rollers will also induce rubbing, instead of simple rolling, which will eat away at axle shafts and cages.
Has anyone approached this company to inquire into their producing a Hyatt type bearing, or to at least make new rollers? Making the cages to hold new rollers would be far less costly than making everything from scratch.
Re: Hyatt Bearings (almost)
Posted: Thu Feb 15, 2024 12:48 pm
by jab35
Well, won't be buying any of those Bitcoins.
So, in 1919 Ford made 12.65 million axle bearings and used 20,396 miles of Type D Chrome Vanadium steel ribbon to form the 102 million spiral rollers. According to the Ford price list for Aug 1919 the bearings sold for $1.00 each (sleeves were $0.30). Adjusting for inflation, bearings in 2024 $ are worth $17.83; sleeves, $5.35. Irrelevant fact having nothing to do with current considerations regarding manufacturing replacement 'Hyatt' type bearings.
However if one could purchase ready made rollers from the bearing company for say $5.00 each ($40/assembly) and make the cages and assemble for say an additional $60.00?? That $100 manufacturing cost (+ $30 for the sleeve); $200 retail?? might be competitive with the "modern replacement assembly" bearing or with the safety hubs on price. I know, lots of if's and assumptions, and I'm not advocating against any current products or safety items. I'm thankful for the availability of these parts and acknowledge all the investment and effort it takes to supply them. Just askin. Respectfully, jb
Re: Hyatt Bearings (almost)
Posted: Thu Feb 15, 2024 1:06 pm
by RVA23T
Mark Nunn wrote: ↑Thu Feb 15, 2024 11:06 am
Making bearing sleeves a smidge thicker would help us use worn bearings.
and that would seem to be an easier change than thicker axle shafts suggested in an above previous posting.
Re: Hyatt Bearings (almost)
Posted: Thu Feb 15, 2024 1:26 pm
by John kuehn
For information purposes a modern style outer bearing kit sells for less than $300.00. That included the seals, sleeve and bearing. I wonder if a Hyatt bearing kit could be made and sold as a kit in that price range. I’m thinking the modern kits have bearings in them that are already made and available so that can make a difference in building a Hyatt kit. But I don’t think Ford ever offered a Hyatt bearing kit. Just an observation to add to the post.
Sleeves are available for the Hyatts but making the Hyatt style bearing becomes the big factor in building them and that’s where the cost comes into play as most of us know.
I haven’t used the modern style replacements so the question is do they last as long as the Hyatts?
Re: Hyatt Bearings (almost)
Posted: Thu Feb 15, 2024 1:27 pm
by Jerry VanOoteghem
Jerry VanOoteghem wrote: ↑Thu Feb 15, 2024 11:43 am
A Hyatt bearing with rollers undersize is not sooo bad. What is bad, is using Hyatts when the rollers are tapered, which is all too common. Tapered rollers will cause the bearing cages to skew/twist, which is what loosens the cages. Tapered rollers will also induce rubbing, instead of simple rolling, which will eat away at axle shafts and cages.
Looking further at the effects of tapered Hyatt rollers...
Let's say we have a bearing with .003" taper in the rollers, and say that one end is .500" dia. and the other is .497" dia. Doesn't seem so bad, right?
Circumference at the .500 end is .5 x 3.141592 = 1.5757"
Circumference at the .497 end is .497 x 3.141592 = 1.5614"
Circumference of the axle shaft is 1.062 x 3.141592 = 3.3364"
So, one revolution of a .003" tapered roller means that one end will want to travel 1.5757", while the other end only travels 1.5614, a difference of .014". One end wanting to "get ahead" of the other end induces a twist on the cage and rubbing/drag on the axle shaft & sleeve. Consider also that given the ratios of roller circumference to axle circumference, each roller turns just over 2 revolutions per 1 axle revolution. Therefore, one or the other end of a .003" tapered roller is dragged over .028"
per 1 axle revolution. In hundreds of miles, how much damage will be done?

Re: Hyatt Bearings (almost)
Posted: Thu Feb 15, 2024 1:36 pm
by Jerry VanOoteghem
RVA23T wrote: ↑Thu Feb 15, 2024 1:06 pm
Mark Nunn wrote: ↑Thu Feb 15, 2024 11:06 am
Making bearing sleeves a smidge thicker would help us use worn bearings.
and that would seem to be an easier change than thicker axle shafts suggested in an above previous posting.
I am assuming that the sleeves are made from commonly available gauges of steel. "Just a smidge thicker" may not be available in a standard gauge thickness, while axles can be made to any size you want, although they too are most likely made from a 1.062" stock diameter. It may be necessary to start with 1.125 stock and turn down to an oversize bearing journal.
All kind of a moot point anyway, since worn rollers don't typically wear evenly across their entire length and cages don't stay tight. You'd be just as hard pressed to search out just the right size of worn bearings to suit your oversize axle, (or thicker sleeves), with even wear across the whole bearing and with tight cages.
Re: Hyatt Bearings (almost)
Posted: Thu Feb 15, 2024 7:36 pm
by Art M
My thoughts is to keep the clearance loose. Everyone wants to have no looseness. These bearings need radial clearance in order to control the roller. At the minimum at least .005 maybe even .010 inch of radial looseness.
I am in constant contact with the NDH Chief Engineer while these bearing were made. He has a lot of experience with automotive wheel bearings. His comments are the direct on the shaft roller bearings have the clearance built into them and it better be loose. Luckily these are not adjustable after they leave thr factory. In the case of the model t, the outer rings must be have the correct thickness.
His bigger concern is the adjustable front wheel bearings. Older cars are scary because too many mechanics/technicians like to adjust them with no clearance. Typically they should have .001 to .009 inch endplay. That is a hard sell in the service field. Modern cars use integral bearings that are adjusted and lubed for life. Unfortunately, they are expensive to replace.
I am planning to calculate the bearing misalignment under load due to shaft bending and planning to calculate the bearing dynamic capacity and expected life under ideal conditions. I need time to do this.
Art Mirtes
Re: Hyatt Bearings (almost)
Posted: Fri Feb 16, 2024 8:16 am
by Mark Nunn
Jerry VanOoteghem wrote: ↑Thu Feb 15, 2024 1:36 pm
I am assuming that the sleeves are made from commonly available gauges of steel. "Just a smidge thicker" may not be available in a standard gauge thickness...
Jerry, the company I work for buys 300,000 tons of steel each year. We state the thickness range that we require in our specifications. We do not specify a gage. Steel mills want thickness specs, not gage when ordering. That takes interpretations out of the picture. Typically, if we need a new thickness that is not already available, a 40-ton minimum order is enough. It becomes a little more challenging when we need a higher grade steel. Some of the steel we buy has a minimum yield strength of 99,000 psi. It would take a large order to purchase that in a new thickness range.
Re: Hyatt Bearings (almost)
Posted: Fri Feb 16, 2024 8:40 am
by CraneJon
Art M.
Sounds like you are GMI? Old school.
Very interesting subject. I recognize the wear in the end bearing housings and stay away from those rear bearings. The rollers should mic at what dia to be acceptable for installation?
Your discussion of front wheel bearings is a whole different beast. How would you measure the clearance? I tighten them up until the wheel noticeably drags, then back the nut off a quarter turn, or two slots on the nut. Never figured out how many threads per inch that would be.
Jon Crane
GMI 72
Re: Hyatt Bearings (almost)
Posted: Fri Feb 16, 2024 8:46 am
by Jerry VanOoteghem
Mark Nunn wrote: ↑Fri Feb 16, 2024 8:16 am
Jerry VanOoteghem wrote: ↑Thu Feb 15, 2024 1:36 pm
I am assuming that the sleeves are made from commonly available gauges of steel. "Just a smidge thicker" may not be available in a standard gauge thickness...
Jerry, the company I work for buys 300,000 tons of steel each year. We state the thickness range that we require in our specifications. We do not specify a gage. Steel mills want thickness specs, not gage when ordering. That takes interpretations out of the picture. Typically, if we need a new thickness that is not already available, a 40-ton minimum order is enough. It becomes a little more challenging when we need a higher grade steel. Some of the steel we buy has a minimum yield strength of 99,000 psi. It would take a large order to purchase that in a new thickness range.
Mark,
I understand the situation you're in when buying essentially mill runs of steel. I don't believe anyone making Model T bearing sleeves will be ordering 40 tons of steel to their exact spec.
I based what I stated on my recollections of a forum posting by someone at Chaffin's, many years ago, that essentially stated the same. (Not intending here to quote Chaffin's or to speak on their behalf. As I said, just my recollections)
Re: Hyatt Bearings (almost)
Posted: Fri Feb 16, 2024 11:30 am
by Art M
Jon,
The front wheel bearing endplay can be measured with a dial indicator. The base of the indicator is mounted to the wheel flange or to the wheel. The indicator needle is located on the end of the spindle. Push back and forth on the hub and read the needle movement. This method was used in the bearing testing laboratory at NDH until the 1980s.
Your method will work very well. That is the way they were set in service garages. However a fair number of mechanics did not back off the tightness. This caused a lot of bearing failures on the road. Grease lubricated tapered roller bearings must have endplay. Oil lubed tapered ones can be tight. Ball bearings can operate preloaded whether oil or grease lubricated.
Turning the slotted nut by one slot (1/6 turn) changes the endplay by approximately .008 inch. Some cars years ago had cross holes drilled in the spindle. Turning the nut from one hole to the other hole (1/12 turn) changes the endplay by .004 in. The typical thread pitch on spindles is 20 threads per inch.
Art Mirtes
Re: Hyatt Bearings (almost)
Posted: Fri Feb 16, 2024 8:38 pm
by CraneJon
Thank you.
Jon